Norrtälje, Sweden
Your partner for product development in industrial and medical technology
Our Cicor site in Norrtälje, Sweden, offers a range of product development services including product care, test systems, as well as manufacturing and testing.
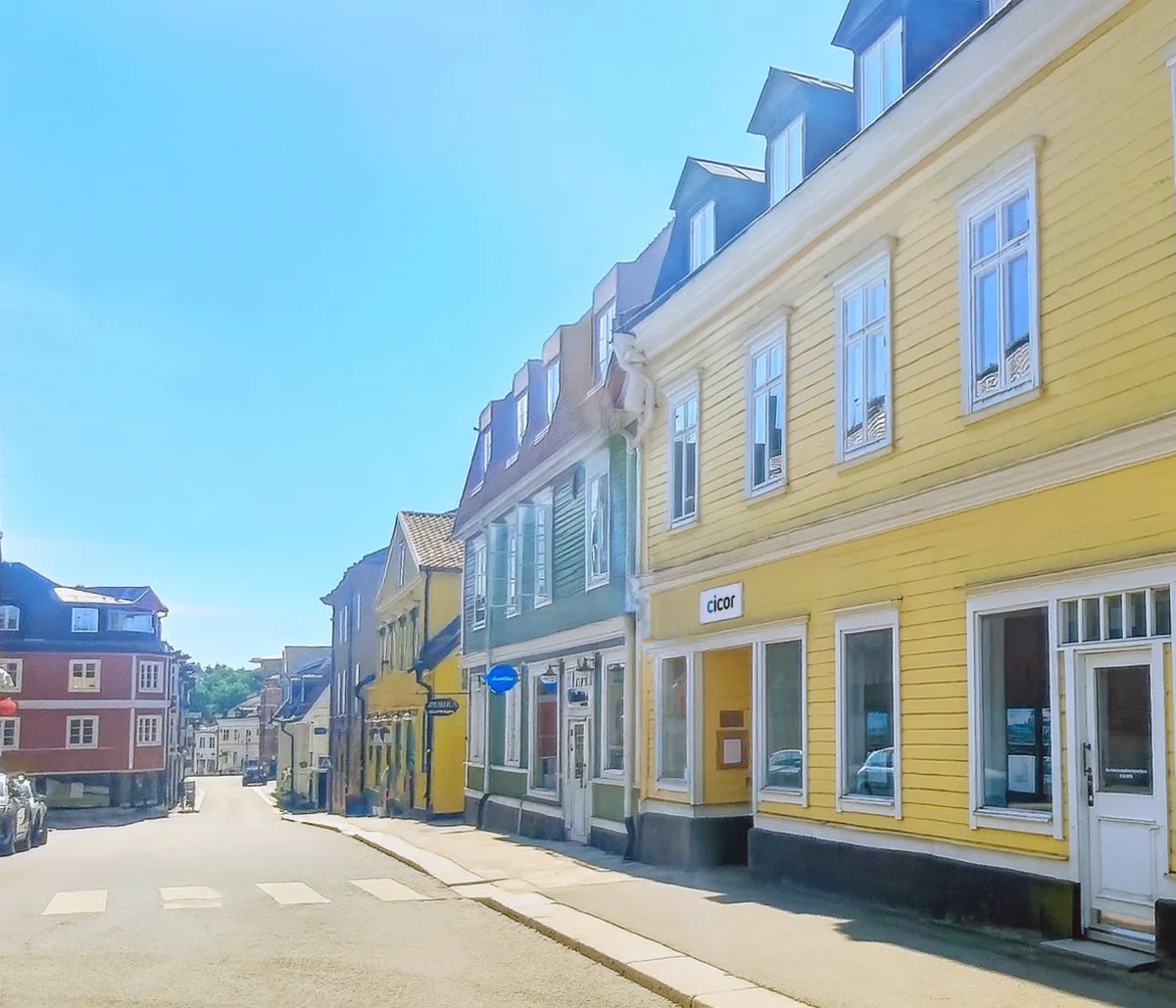
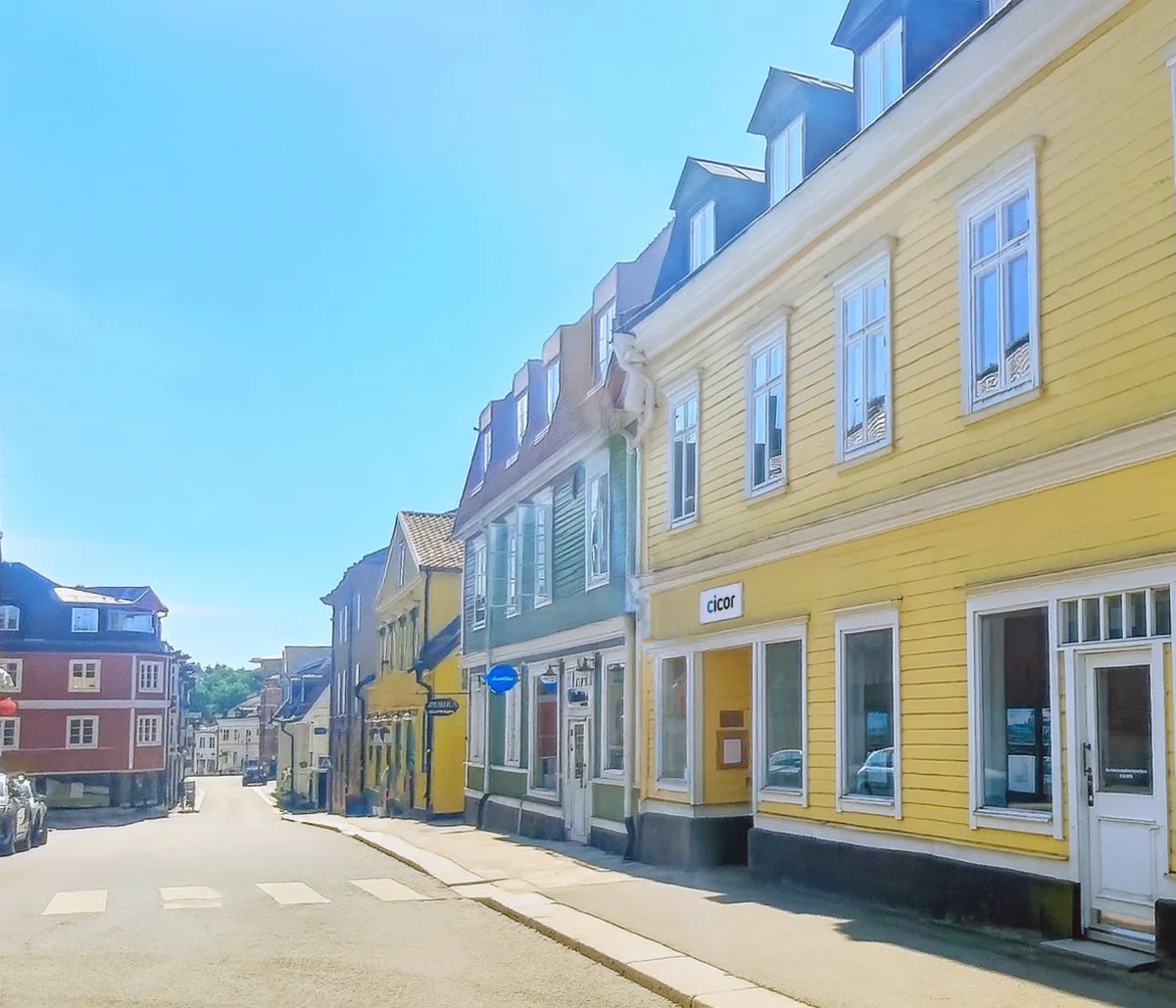
- The site is ISO-13485 and ISO-14001 certified to ensure high quality and environmental responsibility
- 4 design centers/sites located in Norrtälje, Västerås, Solna and Uppsala, Sweden
- Comprehensive services covering Product Development, Test Engineering and Box Building
- Experience of over 40 development engineers
Expertise and Services
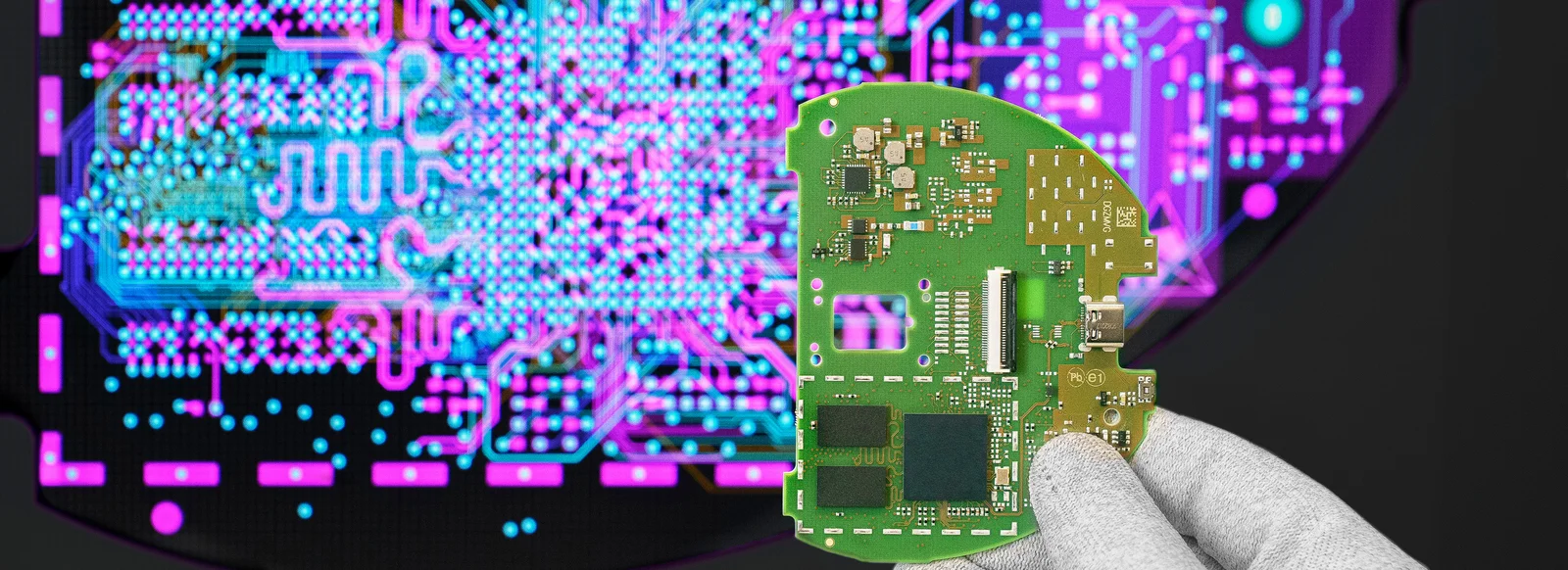
Product Development
We specialise in MedTech, BioTech, Industrial Tech and Defence, providing cutting-edge innovations tailored to the stringent demands of these sectors. Our core competencies include control systems, sensor fusion, and the integration of machine learning, edge AI, and other intelligent technologies.
Our areas of expertise include concepts, project management, product management, electronics, mechanics, software, certification, and industrial design.
Our competent team of experienced engineers and developers is ready to transform your product requirements into a finished production solution. We understand the complexities of medical technology and industry, and we have the expertise to deliver efficient products. We provide comprehensive solutions from concept to finished product, managing every aspect of product development to make the process smooth and efficient for our clients.
Our industry-specific experience in medical technology and manufacturing makes us the trusted choice for companies seeking innovation and high-quality products. We prioritise quality and safety at every stage of the development process, adhering to industry standards to ensure each solution meets the necessary application, legal and quality requirements.

Our ISO-certified product development process is structured in the form of a 'V'. This means that, from the outset, we focus on the latter stages of the product life cycle, where requirements and verification plans are created early on. The process also incorporates risk analysis and mass production planning.
The following steps are typically part of the product development process at Cicor Nordic Engineering.
Step 1: Preliminary study
Every project starts with a feasibility study. This step is crucial in providing you with forecasts relating to the project's resources, timeframe, risks and opportunities, as well as an analysis of design concepts.
Step 2: Execution and integration
At this stage, we begin working closely with your team on the project. By actively participating in your processes, we ensure that our side of the development is transparent and fully visible to you.
Step 3: Evaluation and handover
Evaluation and handover are critical to our mutual success. We conduct a thorough review to guarantee that all aspects of the project have been handled satisfactorily.
Step 4: Support and product maintenance
Once the project is complete, we can continue to support and maintain the product. Our aim is to build a long-term relationship to ensure the product continues to work optimally and meets any changing needs.
The mechanical aspects of a product play a crucial role in the user experience, from opening a compartment to changing a battery or handling a blood sample tube. Smooth and intuitive mechanics are essential for ensuring a product is user-friendly. We create products where the device fits smoothly into place and where the user doesn't need to use excessive force to perform tasks. Our skilled mechanics and industrial designers specialise in areas such as static and moving mechanics, electric motors, pneumatic solutions, and hydraulic constructions, as well as materials including metal, plastic, and wood. We also consider production tools and conduct precise calculations, including FEM (finite element method), to ensure our products are of the highest quality and perform well. Every detail is important in creating a seamless and efficient product.
Programming is an indispensable part of today's product development. Our expertise covers everything from software integration to the other design elements that form the core of a product. This is our specialty, known by various names, such as embedded systems, system development or hardware-related software. We combine in-depth knowledge with user-friendly platforms to guide your development smoothly towards a finished product.
We can handle everything from programming circuit boards to creating applications that control or monitor your devices. Our skills cover MCUs, embedded programming, test system programming, sensor systems, UI/GUI and Edge AI/ML. With us, you get a partner who will simplify your journey to creating your first product by offering versatile expertise and reliable platforms.
We specialise in electronics hardware, focusing on circuit boards and their immediate surroundings. We offer a complete solution, from concept and design to finished prototype and certified product. Our aim is to deliver the first prototype to you quickly so that you can evaluate its application.
Certification and investigation are two critical steps to ensure compliance and quality in various industrial areas. We are a reliable partner specialising in areas such as electromagnetic compatibility (EMC) and the Low Voltage Directive (LVD). We specialise in guiding companies through the certification process, ensuring their products meet the required standards and regulations.
Our expertise extends beyond basic product requirements, and we have successfully obtained certifications in accordance with international standards such as ISO 13485 and ISO 14001. ISO 13485 demonstrates our dedication to the quality and safety of medical technology, and ISO 14001 confirms our commitment to environmentally friendly operations.
These certifications are closely linked and serve as benchmarks for our daily work. By combining expertise in production and medical technology with environmental awareness, we strive to create engineering solutions that are outstanding and responsible. Our ambition is to not only meet market expectations, but also set the standard for quality and sustainability within our industry.
The certification process
At Cicor in Norrtälje, our team of qualified experts has extensive experience in product certification and is ready to support you through every step of the process. We understand that every industry and product presents unique challenges, and our flexible approach ensures your company achieves successful certification tailored to your specific requirements.
Investigation services
In addition to assisting with certifications, we also offer comprehensive investigation services. Our specialists conduct thorough investigations to identify and resolve any issues related to quality, compliance and safety. Our goal is to provide our clients with comprehensive solutions that not only fulfil the necessary requirements, but also improve the efficiency and dependability of their products and processes.
We offer a technical evaluation service for companies and businesses, which involves conducting a thorough analysis and assessment of your existing technical solutions. Following this, we present a list of recommendations to optimise your operations, technology or systems. We also evaluate certification requirements and offer guidance on component selection and strategies. If necessary, we can help you select a production provider and conduct rigorous testing and quality assurance processes. We also carry out life cycle analyses (LCAs) to assess long-term sustainability and environmental impact.
Technical evaluation for certification
Our technical evaluation for certification is aimed at companies that need to ensure their products are secure and efficient. We test your products as prototypes to determine if they are ready for final validation or if their performance requires enhancement. We evaluate whether products meet requirements such as CE marking through the necessary tests and analyses. Our engineers oversee every step to ensure that you can affix a CE mark to your products with confidence and ease.
Technical evaluation for investment: a realistic outlook for future success
We initiate the process with an analysis of the technical architecture to examine how well it supports the company's overarching goals. By identifying its strengths and weaknesses, we can provide a realistic assessment of its ability to scale and adapt to meet future demands.
Our evaluation also includes an analysis of how the system performs under various scenarios, and its ability to scale up to meet increasing demand. This gives investors insight into how the technology can grow alongside the company as it expands and usage increases.
We also focus on security aspects through our security assessment. We proactively identify potential vulnerabilities and security risks to give investors confidence in the robustness of the technology and the level of protection it provides. Our analysis includes recommendations for improving security.
Finally, we evaluate how easily the technology can be maintained and upgraded over time to support long-term success.
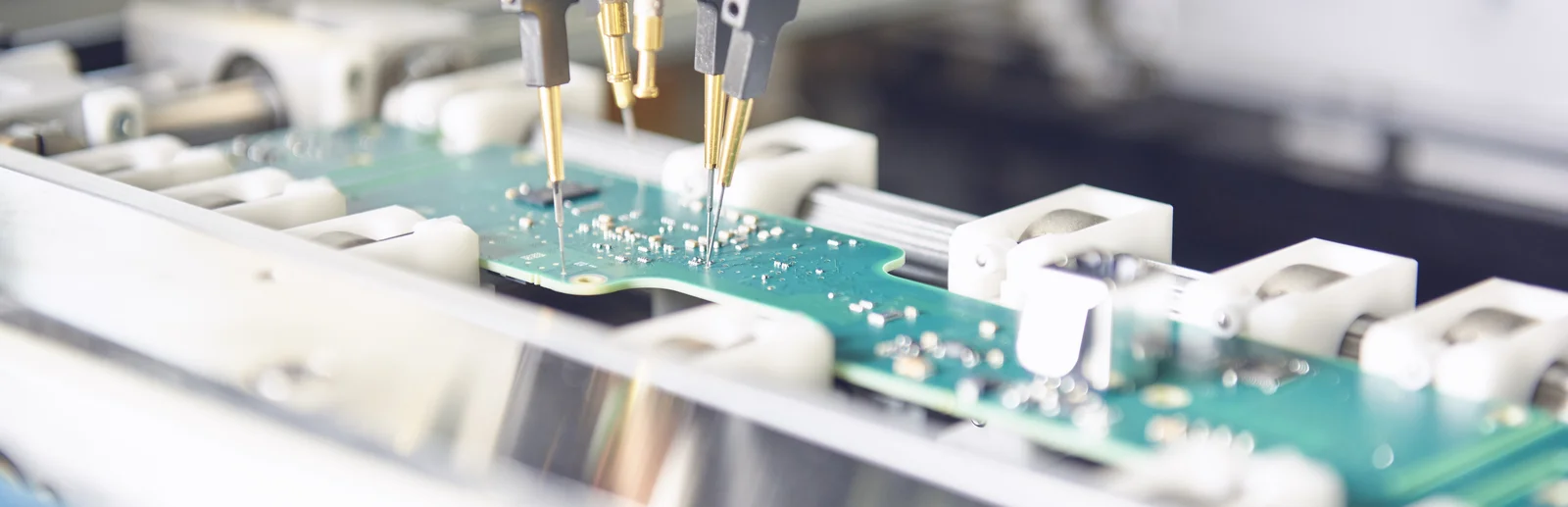
Test Engineering
We offer customised testing systems to ensure high production quality. We also develop cost-effective, standardised test systems for the MedTech and other industries.
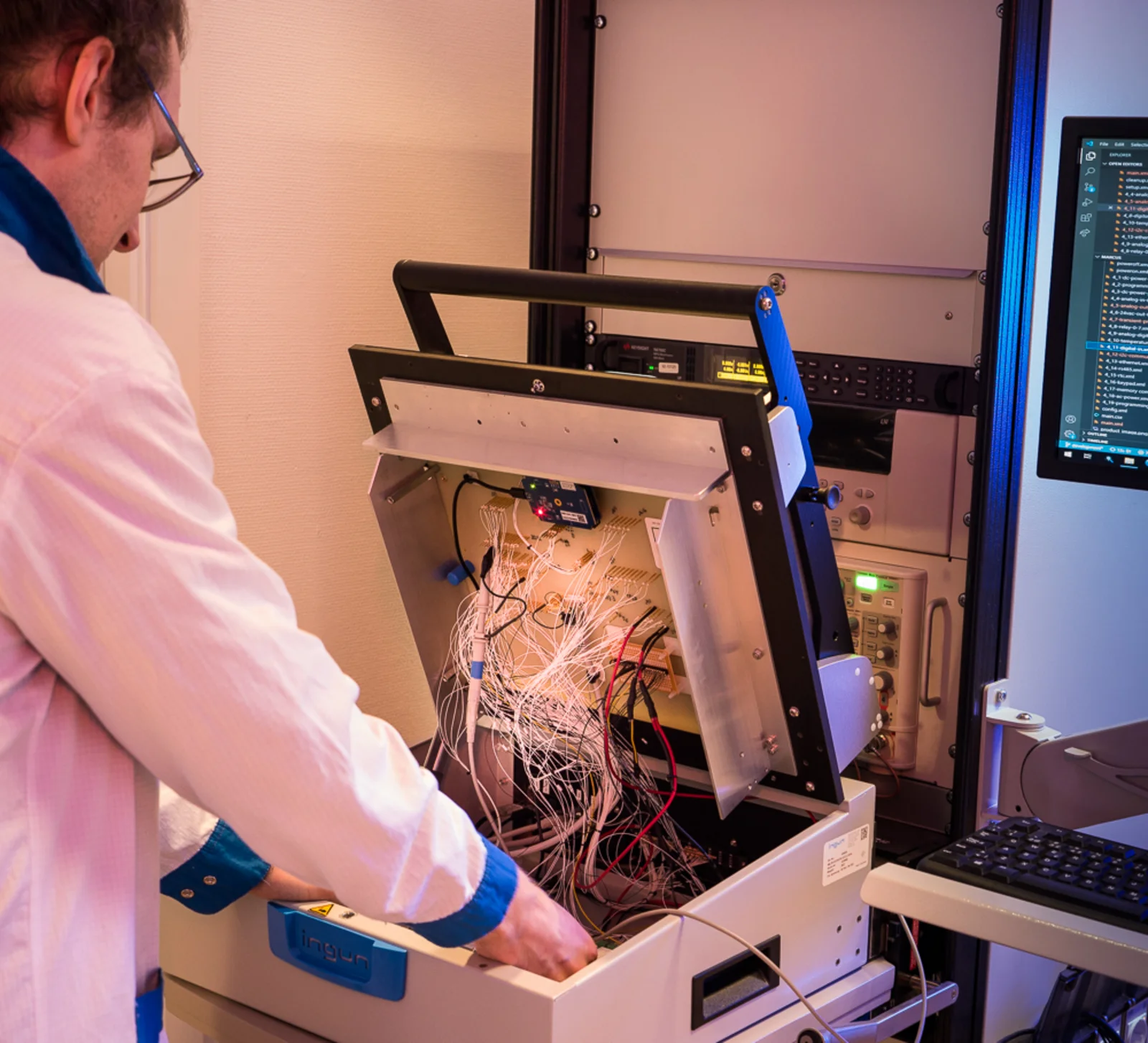
The Rack Test System (RTS) is a high-performance testing solution that has been designed to streamline and simplify the testing of products within a variety of industries and product categories. Based on a rack-mount architecture, it integrates test instruments and system components into a unified platform. The RTS offers companies and organisations that require accurate and efficient testing of their products in a laboratory or production environment a number of advantages.
By integrating multiple test instruments into a single platform, the RTS reduces changeover times and increases test productivity, resulting in cost savings and faster product manufacturing.
The RTS is a flexible, scalable, and compact test platform. It supports multiple product types via swappable fixtures and integrates high-performance instruments such as oscilloscopes and signal generators. Automated functions boost speed, accuracy and efficiency, and there are options for production line integration. Its rack-mounted design saves space, and testing can also be performed off-site in our laboratory.
Designed to make testing more efficient and cost-effective for companies and organisations striving for the highest product quality, RTS is a powerful and versatile testing solution. Thanks to its scalable design, advanced test instruments and automated functions, the RTS is a valuable tool in sectors such as electronics, telecommunications, medical technology, automotive and industrial automation.
Like all our test systems, the Rack Test System (RTS) can be connected to our cloud-based test database (TestNet), allowing you to monitor the latest results in real time and easily extract test protocols for a specific unit. This allows you to achieve very high traceability in your production and test results. We offer customised test systems to ensure high production quality. We also develop cost-effective, standardised test systems for the MedTech and industrial sectors.
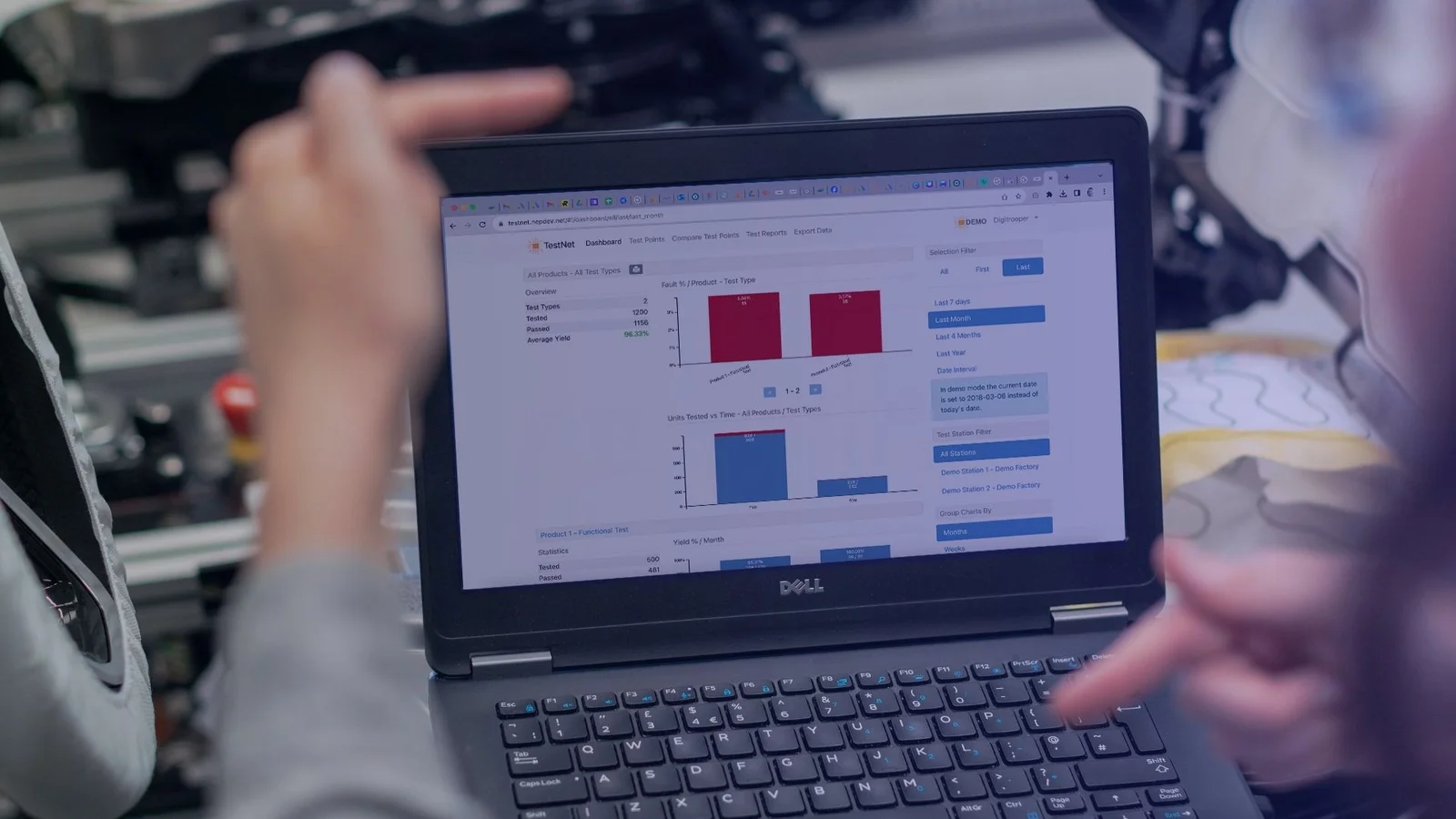
Our TestNet provides an efficient solution for optimising production control. By integrating this test data management system into their production facilities, companies can easily monitor the production process in real time, eliminating the need for physical presence. This enables deviations to be identified and managed quickly.
Real-time quality control
One of the key advantages is the ability to perform real-time quality control. TestNet provides companies with an overview of error occurrences and analyses why certain units fail to meet product and test requirements. This insight enables companies to take swift action to enhance product quality and ensure compliance with standards.
Detailed test protocols are another benefit of the TestNet
The system also facilitates the creation of detailed test protocols for each unit, enhancing product traceability. This allows companies to meticulously track the progress of each unit throughout the production process.
Another advantage is the ability to analyse overall test capacity. TestNet provides your company with the opportunity to track trends and identify changes in production quality and speed. It also helps to quickly detect bottlenecks in the production process and optimise production goals.
The TestNet also enables comparisons between different production units. It provides valuable insights that can be used to implement best practices and optimise the production process across the entire organisation.
Panels and graphs
From the instrument panel, you can access an image showing a Pareto diagram of the most common errors for current products, for example. By offering various types of diagrams and trend analysis, TestNet provides an overview of common errors and enables continuous improvement. This analysis provides you with the tools to make informed decisions and minimise errors in the production process.
Finally, the TestNet provides you with access to a real-time database, giving you the latest information you need to make informed and prompt decisions based on the current production status.
Reliable test systems are essential for ensuring the high quality of electronic components and products. The design of a test system can vary significantly depending on the product and its specific testing requirements. It has therefore become increasingly important to develop fully customised product testing systems that are tailored to meet the exact needs of customers.
With our fully customisable test systems, we can ensure they fit into your production line.
We design the test facility based on the product.
When developing a product test system, we always start with the customer’s specific requirements. This means there is no one-size-fits-all solution: each test facility is designed to suit the product or component to be tested. This flexibility enables us to handle a wide variety of products. Our system can also verify parameters other than purely electrical ones, such as pressure, flow, specific steps, movement and temperature.
Creating a fully customised product testing system begins with a careful analysis of the customer’s needs and product specifications. No detail is too big or too small. Next, our experts create a detailed design that includes everything from test procedures to software interfaces.
We take this into account when designing a complete test system.
The test procedures are developed according to the customer’s requirements and are designed to evaluate every aspect of the product thoroughly. These may include function tests, performance tests, continuity tests and much more besides. With our system, we can also verify parameters other than purely electrical ones, such as pressure, flow, specific steps and temperature.
The selection of test equipment is crucial.
A wide range of measuring instruments and test equipment is crucial to ensure accurate and reliable testing. The software that controls the test system has been adapted to facilitate communication with the customer’s system, as well as the collection of test data and the presentation of results in a user-friendly way. We also have our own software for test systems.
Automation and machine learning
Automating the testing process is often a key feature, especially when handling large volumes of testing. This may include automated sampling, report generation and remote monitoring. We can also offer image processing with machine learning for use during production tests. This allows us to verify that the wiring has been correctly assembled, the correct amount of solder has been applied and that the radiated field (electromagnetic radiation/EMC) is at the correct, approved level.
Image analysis also verifies the behaviour of any moving parts. The test system is designed with security and reliability in mind.
Once the fully customised product test system has been designed and implemented, extensive testing and quality control procedures are performed to ensure that it performs in accordance with the specifications. Among other things, we carry out clean insulation tests and earth continuity tests to ensure that the product meets all standards. If desired, we can also obtain CE approval for the test system in relation to the Machinery Directive and the Low Voltage Directive. The test facility is only put into operation once the customer is satisfied with the result.
Invest in quality and efficiency with fully customisable test systems.
These systems are a valuable investment, ensuring that every electronic component or product that goes through the testing process is of the highest standard. They ensure that every electronic component or product that goes through the testing process meets the highest standards. With our dedicated, customer-centred design process, you can rest assured that your testing requirements are in safe hands and that your products are ready to meet market demand.
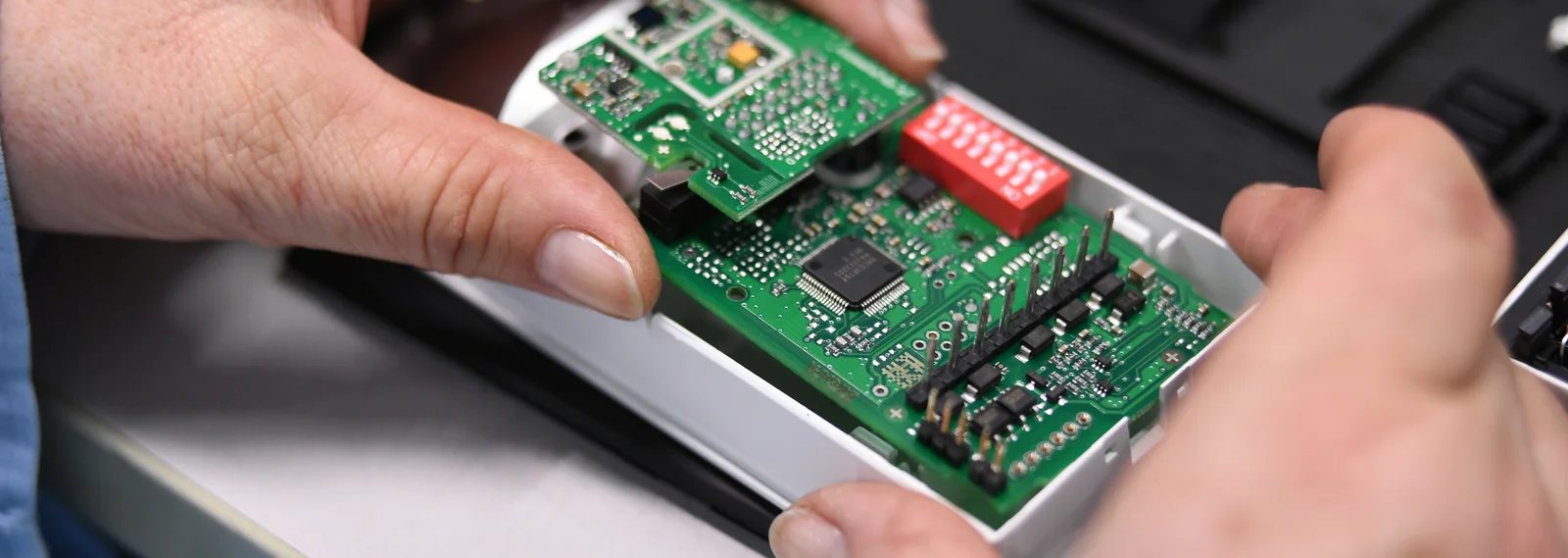
Electronic Manufacturing Services
Our electronic manufacturing services are designed to deliver exceptional flexibility, speed and quality, with a dedicated focus on prototypes and low-volume production. Our adaptable assembly lines enable us to offer rapid setup and quick responsiveness to evolving project requirements. We operate under ISO 13485-certified processes and within a clean room environment (ISO class 7) to ensure compliance with the highest standards, particularly for medical-grade products.
We offer comprehensive manufacturing and material handling services for those who have developed their own product, whether with or without our assistance. We understand the importance of testing the market and optimising your product before entering into full-scale production. To support you in this critical initial stage, we have created a small-scale project manufacturing service, which we tailor to each customer's specific requirements.
Our product manufacturing service is designed to meet your needs when large-scale production is not yet feasible. We recognise the importance of flexibility in production and the ability to adapt to market demand. With our service, you can manufacture smaller or larger quantities at a time, allowing you to test the performance of your product and the market response before taking the step into large-scale production with our support.
Our experienced personnel and control systems ensure high-quality manufacturing and material handling. Our goal is to deliver results that will help you establish a strong market presence for your product.
There are several advantages to starting production with a limited quantity of units when launching a new product. Firstly, it allows you to test the market before committing to large-scale production. Manufacturing in small quantities enables you to obtain valuable customer feedback, identify areas for improvement and customise the product as required.
This method also minimises initial economic risks. If the product does not meet expectations or adjustments are needed, the cost of making changes is significantly lower than if you were managing large inventories. Small volumes also allow for a quicker product launch, enabling you to start generating revenue while refining the product based on customer feedback.
In summary, manufacturing according to our model at the beginning of the product lifecycle is a strategic way to minimise risks, optimise the product's alignment with the market and enable a smoother, more successful launch.
Automation Solutions
- Robot Cells -Customized and Integrated Solutions for Automated Production
- Advanced manufacturing equipment
- Automated and Integrated Manufacturing -Streamlining Production Flows
- Optimized Prototyping and Series Manufacturing -DFxAnalysis for Cost-Effective Production
- Vision and Sensor Systems -Advanced technology for quality control and precision control
- Industrial IoT and Connected Systems -Smart solutions for data management and predictive maintenance
Testsystem
- Test concept
- Standard and customer specification test systems
- Integration of test systems into the production environment
- Quality data management with traceability through the entire product life cycle
Product Care
We take care of your released products, address component shortages as they arise, or handle the need for redesign. We also conduct technical investigations.
Component shortages and component replacement in existing products
Replacing components in an existing product is akin to swapping a piece in a puzzle – it must be done with precision to ensure the final result fits perfectly. Our organization is adept at rapid deployments and interventions when a "crisis" arises in development, in the field, or during production.
Replacing components in a functioning product always entails some risk. Therefore, we recommend avoiding it if possible, but when necessary, we execute replacements without compromises. A thorough examination is crucial for achieving optimal performance when switching components. Our experts conduct meticulous assessments to ensure component replacement not only functions but also enhances the product's performance. It's like creating a perfect symphony of components working together in harmony.
Replacing components
While seeking assistance may seem like an investment, professional expertise often leads to more cost-effective long-term solutions. By avoiding mistakes and inefficient choices, both costs and lost time are minimized. Component replacement can also be sensitive regarding regulations and standards. Therefore, we ensure all actions comply with industry regulations.
Safety during component replacement
For companies prioritizing safety, it's crucial to replace components in a way that doesn't compromise product safety.
We ensure replacement components meet and exceed safety standards, providing your company and customers with maximum confidence.
Quality of components
Another aspect is lasting quality. A well-developed component replacement plan includes rigorous testing to ensure the new component maintains the same or higher quality than its predecessor. This helps extend the product's lifespan and reduce the risk of future issues. Hence, we assist companies in navigating the maze of different component options.
We consider compatibility, availability, and cost aspects to ensure you get the most suitable components without unnecessary delays or surprises.
Getting help with component shortages or component replacement is like having a reliable guide through a complex journey.
Handling manufacturing issues for smooth production
Sometimes the manufacturing process can halt for various reasons, such as quality issues, component shortages, or third-party problems. We understand the complexity of these situations and are here to offer solutions to keep your production running. Whether it's managing quality issues, overcoming component shortages, or navigating challenges with external suppliers.
Technical solutions and production relocation
Our team of experts can provide technical solutions to address specific issues that have arisen in your manufacturing process. We also have experience in successfully relocating production, a strategy that can ensure continuity and efficiency in your operations. Ensuring a good match between the product's needs and the manufacturer's capabilities is becoming increasingly crucial for a long-term and sustainable manufacturing situation.
Urgent component shortage
In an urgent situation, our expertise in CAPA and 8D methods is an asset that ensures the problem is not only temporarily resolved but also prevented from recurring. It is our collective endeavor to ensure your production returns to its optimal level and remains sustainable over time.
Component swaps and actions with CAPA, 8D methods
If you're facing the challenge of replacing components that are no longer available, we can assist you with a comprehensive solution. We utilize advanced methods such as CAPA (Corrective and Preventive Actions) and 8D (Eight Disciplines) to systematically identify root causes and implement long-term and sustainable solutions.
These methods serve as tools for analyzing and solving complex production problems. By applying them, we, together with you, can identify the problem and develop an action plan to address it.
Investigation with fault and improvement analyses
Are you seeking solutions for product, production, or field return issues? Our expertise lies in fault investigations, where we meticulously analyze technical problems to understand their root causes and potential. We provide tailored solutions for both immediate and long-term resolutions.
We specialize in 8D reports, utilizing a structured method to identify, analyze, and solve problems. By applying this methodology, we ensure not only an effective fault investigation but also sustainable problem resolution.
Whether it's production deviations or recurring field returns, we approach each challenge with a professional and dedicated mindset. Our goal is to offer not only a swift solution to the current problem but also to implement measures that minimize the risk of future issues.
Customized product care services
At Cicor Nodric Engineering, we offer tailored product care services designed to ensure delivery capability and product quality in mass production. Our aim is to help you avoid unnecessary production halts by providing services such as cost rationalization, technical product management, and component updates.
Support through the entire process
We handle the entire process, from searching for replacement components to implementing software updates to enhance functionality and meet the latest regulations and certification requirements. Additionally, we provide application support and documentation for complete traceability and increased transparency.
Phasing out, transitioning, or replacing products?
Our expertise extends to phasing out existing products, transitioning to new generations, or seamlessly switching to other products. We understand the importance of maintaining a sustainable product lifecycle, focusing on ensuring your products remain competitive and meet market demands.
Within our product care operations, we strive to offer a broad and customized service to ensure your products maintain the right quality and performance.
Services we provide within investigations, analysis, and product care
- Cost rationalization for mass-produced products
- Product and production support, including technical product management
- Component updates in case of shortages or outdated components
- Search for replacements and exchanges
- Develop an equivalent solution with minimal design changes if necessary
- Software updates to meet the latest requirements and standards
- Regular updates and monitoring to ensure compliance with guidelines
- Updates and application support for existing customers and new markets
- Phasing out to new generations or alternative products
- Establishing efficient service and maintenance of products in the field and in manufacturing with data management and ML/Edge-AI
- Life cycle analysis (LCA)
- Establishing and maintaining testing systems for manufacturing
Proactive product care with NEP
Our proactive strategy involves continuous monitoring of product quality and implementing preemptive measures to ensure your products maintain a high standard over time. We understand the importance of creating a smooth and worry-free product care process for our customers. By entrusting product care to Cicor Nordic Engineering, you can be confident that your products are handled professionally and with precision. Our dedication to proactivity and quality makes us the obvious choice for companies seeking a reliable and efficient product care partner.
Production control with TestNet
TestNet offers your company an efficient solution to optimize production control. By integrating this test data management system into production facilities, companies can easily monitor the production process in real-time without needing to be physically present. This enables the quick identification of deviations and immediate management thereof.
Real-time quality control
One of the key advantages is the ability for real-time quality control. TestNet provides companies with an overview of error occurrences and analyzes why certain units fail to meet product and test requirements. This insight enables swift actions to enhance product quality and ensure compliance with standards.
Detailed test protocols with TestNet
The system also facilitates the creation of detailed test protocols for each unit, enhancing traceability of the products. It enables the company to meticulously track the progress of each individual unit throughout the production process.
Another advantage is the ability to analyze the overall test capacity. TestNet provides your company with the opportunity to track trends and identify any changes in production quality and speed. It also helps quickly detect bottlenecks in the production process and optimize production goals
TestNet also enables comparisons between different production units. It provides your company with valuable insights to implement best practices and optimize the production process across the entire organization.
Panels and graphs
From the instrument panel, you receive, for example, an image showing a Pareto diagram of the most common errors for the current products. By offering various types of diagrams and trend analysis, NEP TestNet provides you with an overview of the most common errors and enables continuous improvement. This analysis gives you tools to make informed decisions and minimize errors in the production process.
Finally, with TestNet, you gain access to a real-time updated database, providing you as a user with the latest available information to make informed and prompt decisions based on the current production status.
CoGS (Cost of Goods Sold) - Reduction of manufacturing cost
COGS, which stands for Cost of Goods Sold, represents the expenses directly associated with the production of your product and typically includes costs such as raw materials, labor, production costs, as well as the cost of distributing and selling the product.
Reducing COGS is a strategic measure that can increase your profitability by improving the gross margin. By streamlining manufacturability, negotiating better prices with suppliers, optimizing inventory management, or implementing cost-saving technologies, we can assist your company in lowering its COGS.
It is important to note that COGS reduction should be carefully balanced to avoid negative effects on product quality or customer satisfaction. Cutting costs must not compromise the value and performance of the product or service. However, a well-planned and strategic approach to COGS reduction can help increase profitability and competitiveness in the market.
COGS reduction within medical technology
When it comes to COGS within medical technology, it's crucial to balance cost reduction with high standards for product quality and compliance with regulations in the healthcare sector.
Quality and safety standards
Medical technology products must meet current quality and safety standards. When reducing COGS, it is therefore crucial to ensure that cost reductions do not compromise the quality of the products or their compliance with regulations.
We help you stay abreast of regulations and guidelines to avoid regulatory issues.
By investing in innovative and cost-effective technologies, companies within medical technology can improve their production process and thereby reduce COGS. However, it is necessary to monitor and validate these technologies to ensure they meet industry standards.
Long-term perspective in the production process
Precision in material selection and negotiation skills with suppliers are crucial for optimizing COGS. We assist you in securing competitive prices for high-quality raw materials.
A thorough review of the production process can uncover opportunities for streamlining and cost reduction. Automation, lean production, and other efficiency improvements should be considered with the goal of maintaining high product quality.
When reducing COGS within the framework of medical technology products, we always strive for long-term sustainability through continuous monitoring and adaptation to changes in the market and technology.
COGS reduction within industrial technology
When it comes to COGS (Cost of Goods Sold) within industrial technology, it's important to strategically manage costs to enhance profitability and competitiveness.
Below are aspects that we consider in COGS reduction within industrial technology.
Streamlining the product's design and production workflows is a priority to reduce production costs, which may involve investing in modern technology to achieve automation. We can assist you in negotiating favorable agreements with suppliers to ensure competitive prices and availability of high-quality raw materials. Efficient use of energy and other resources is also crucial, not just economically but also environmentally. This may involve energy-saving measures and material recycling to reduce COGS.
Another important aspect of COGS reduction is the opportunity to increase production volume and thus decrease unit costs. This requires careful analysis of market trends and demand. It is important to continuously evaluate and analyze the production process and cost structure to identify opportunities for improvement and cost reduction over time. By considering these factors together, your company in medical or industrial technology can effectively achieve cost savings without compromising quality and compliance.
Cases
Work with us
Join the Cicor site in Norrtälje, Sweden! We are always on the lookout for new talented people and would be delighted to receive your application.
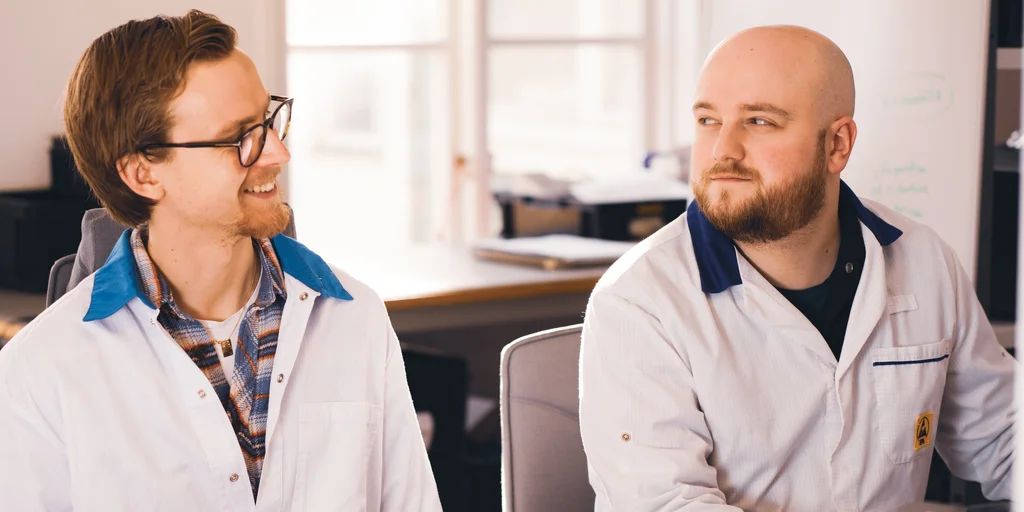